Our Solutions
Hand Lay-Up Process (Traditional & Customizable)
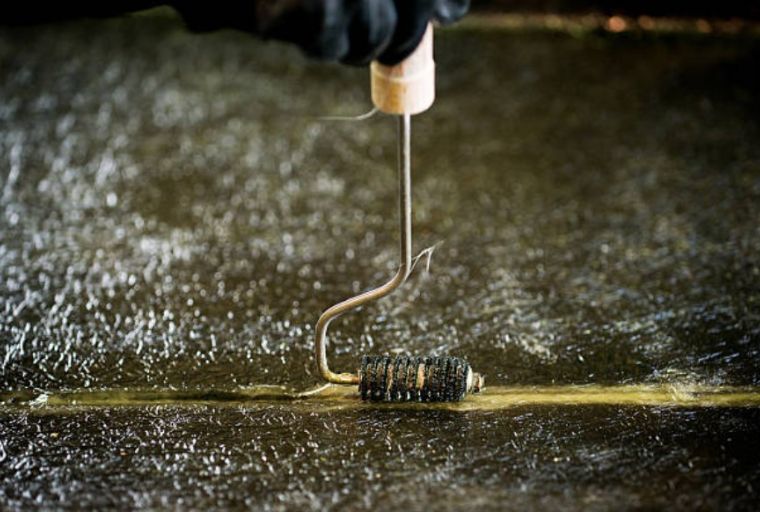


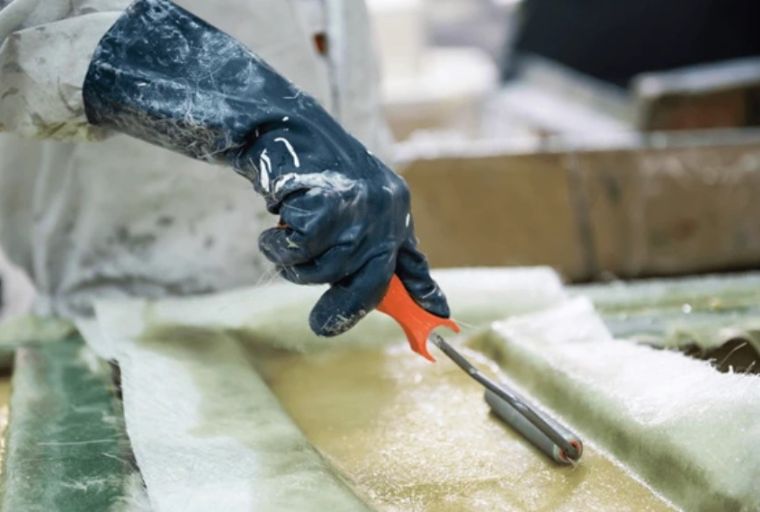

Purpose
The Hand Lay-Up process is a traditional manual method used for manufacturing fiberglass-reinforced plastic (FRP) parts. It is widely used for producing large, complex, and custom-shaped parts in industries such as automotive, marine, construction, and industrial applications.
In this process, fiberglass reinforcements (mats or woven fabrics) are manually placed into a mold, and liquid resin is applied using brushes or rollers. The part is then left to cure at room temperature or with controlled heat.
Advantages
✅ Cost-Effective for Low-Volume Production: Requires minimal equipment, making it ideal for small and medium production runs.
✅ Design Flexibility: Can produce customized, complex shapes without high tooling costs.
✅ Good Mechanical Strength: Properly layered parts provide strong and durable structures.
✅ Scalability: Suitable for both prototypes and large components.
✅ Material Versatility: Compatible with various resins and reinforcements to meet specific application needs.
✅ Ease of Implementation: A straightforward process that does not require advanced automation.
This method is particularly suited for large parts like boat hulls, vehicle body panels, industrial covers, and decorative elements where precision and customization are key.
Steps:
- Mold Preparation – The mold is cleaned and coated with release agent to prevent adhesion.
- Gelcoat Application – A gelcoat layer is applied for surface protection, smoothness, and aesthetic finish.
- Fiberglass Placement – Layers of fiberglass mat or fabric are manually placed into the mold.
- Resin Application – Resin (typically polyester, vinyl ester, or epoxy) is brushed or rolled onto the fiberglass.
- Lamination & Air Removal – Using rollers to ensure complete saturation and remove air bubbles for a strong, uniform part.
- Curing – The part hardens at room temperature or in a controlled oven, depending on resin type.
- Demolding & Finishing – The part is carefully removed from the mold, trimmed, sanded, and inspected for quality control.
Light Resin Transfer Molding (LRTM)
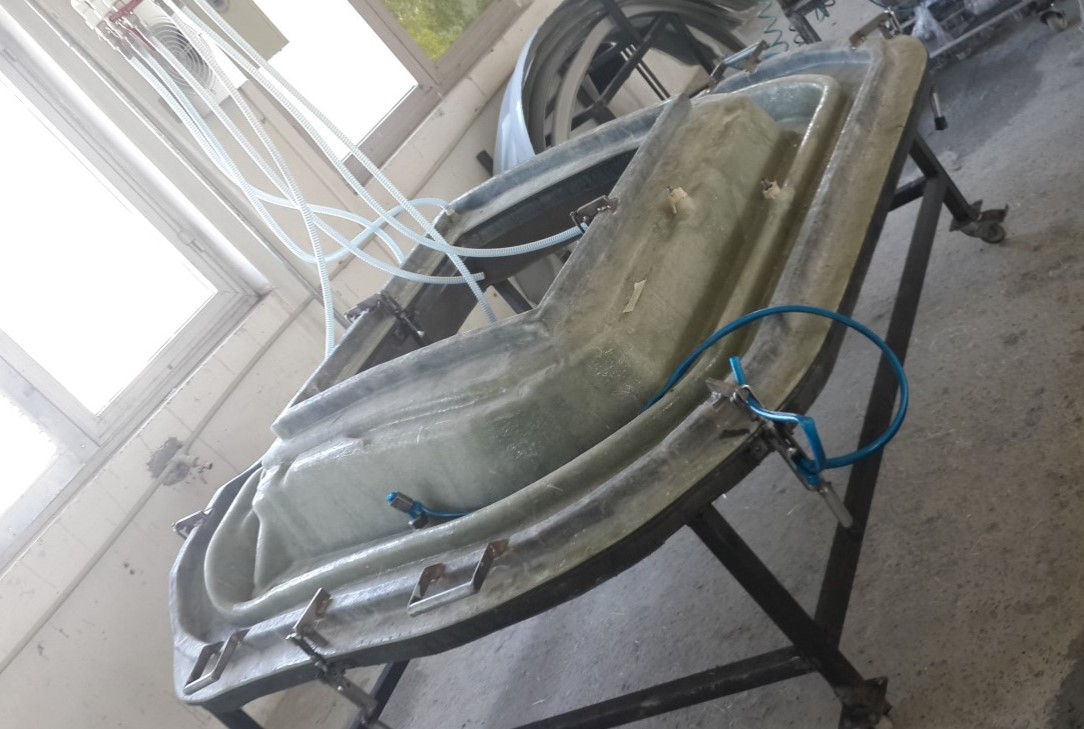




Purpose
The Light Resin Transfer Molding (LRTM) process is an advanced closed-mold manufacturing technique used to produce high-quality composite parts. It is designed for medium to high-volume production, offering improved consistency and surface finish compared to open-mold methods like Hand Lay-Up.
In LRTM, dry fiber reinforcements are placed inside a closed mold, and resin is injected under vacuum pressure, ensuring even distribution. The part is then cured inside the mold, resulting in a high-strength, lightweight, and precise component.
Advantages
✅ High-Quality Surface Finish: Both sides of the part have a smooth, controlled finish (ideal for visible components).
✅ Better Resin Control: Reduces excess resin, leading to lighter and stronger parts.
✅ Improved Dimensional Accuracy: The closed mold ensures high precision and repeatability.
✅ Higher Production Efficiency: Faster cycle times compared to Hand Lay-Up, making it ideal for batch production.
✅ Reduced Emissions & Waste: Lower VOC (Volatile Organic Compound) emissions and minimal material waste contribute to an eco-friendlier process.
✅ Consistent Mechanical Properties: Controlled resin infusion enhances part strength and durability.
LRTM is widely used in industries such as automotive, rail, marine, and industrial manufacturing, where lightweight, high-strength, and visually appealing fiberglass parts are required.
Steps:
- Mold Preparation – A two-part mold is cleaned, coated with release agent, and loaded with fiber mats preforms.
- Mold Clamping – The mold is closed and sealed to create a controlled cavity.
- Resin Injection – Resin is injected under pressure, evenly saturating the fibers reinforcement.
- Curing Inside the Mold – The part cures inside the closed mold, ensuring precise shape and mechanical properties.
- Demolding & Finishing – The finished part is removed, edges are trimmed, and the surface is polished.
- Quality Inspection – Dimensional checks and mechanical testing ensure compliance with client specifications.
Resin Infusion
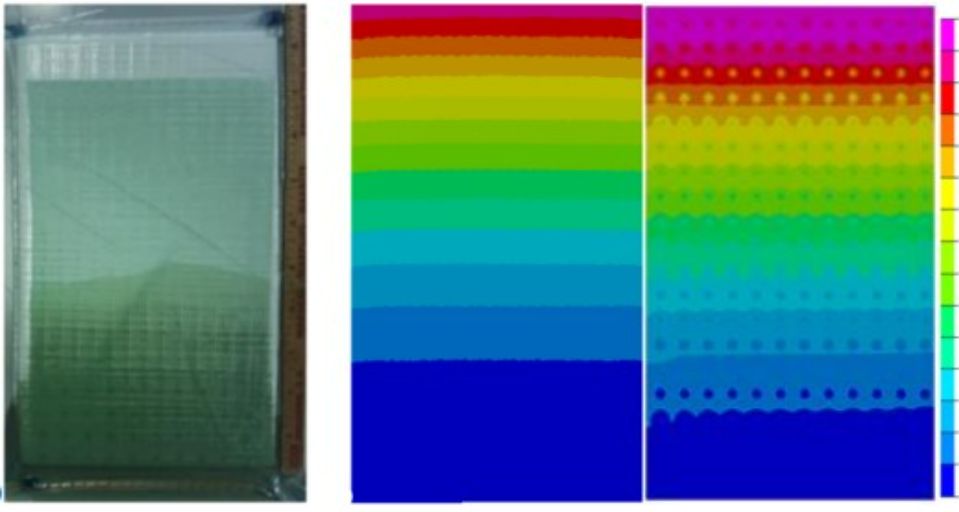
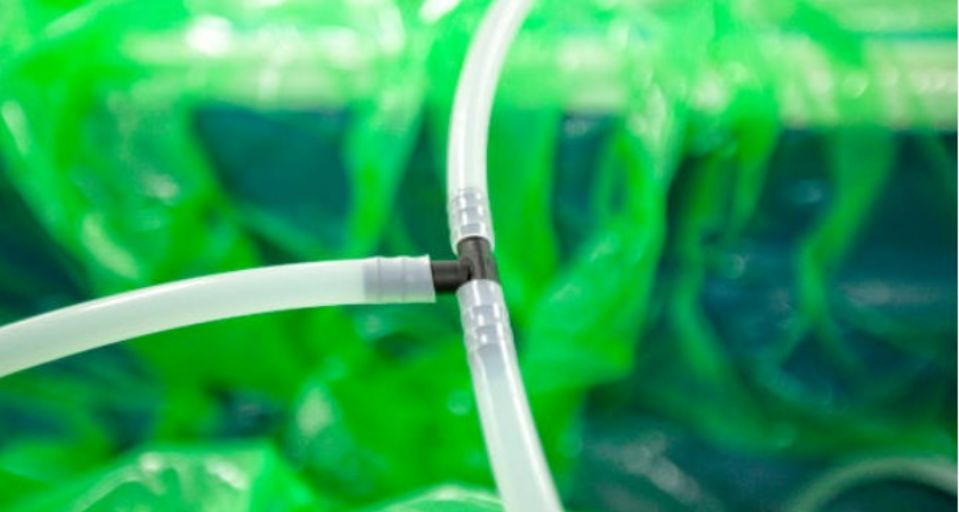
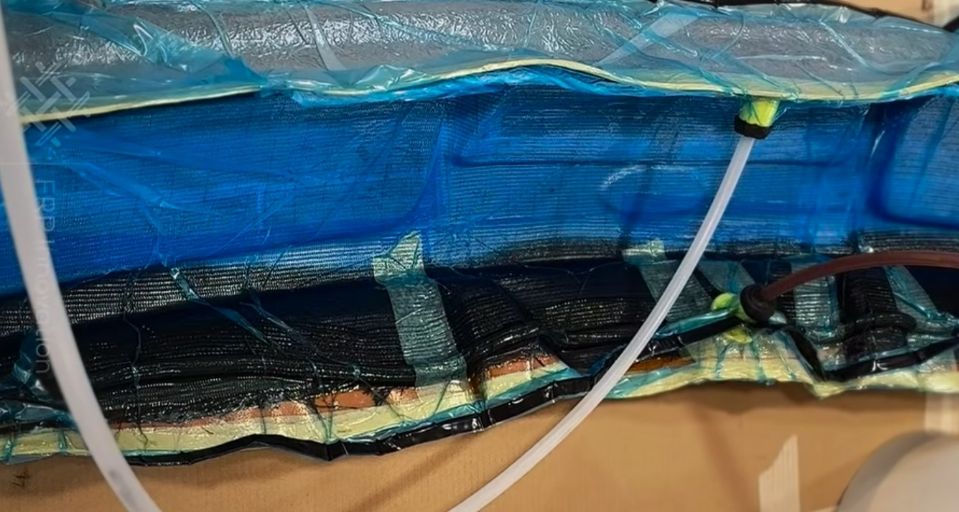
Purpose
The Resin Infusion Process is an advanced closed-mold technique used to produce high-strength, lightweight, and high-quality composite parts. This method is ideal for large, complex, or structurally demanding components in industries such as aerospace, marine, wind energy, and automotive.
In resin infusion, dry fibers reinforcements are placed in a mold, covered with a vacuum bag, and sealed. A vacuum draws liquid resin through the fibers, ensuring a precise and even distribution before the part cures.
Advantages
✅ Superior Strength-to-Weight Ratio: Optimized resin-to-fiber ratio results in light yet highly durable parts.
✅ Excellent Surface Finish: Smooth, controlled surfaces on one side, suitable for aesthetic and functional applications.
✅ Consistent Quality & Structural Integrity: Uniform resin distribution eliminates air pockets and voids, improving mechanical properties.
✅ Reduced Waste & Emissions: Lower resin consumption and minimal VOC emissions make it an eco-friendly process.
✅ Large & Complex Part Capability: Ideal for big components such as boat hulls, wind turbine blades, and structural panels.
✅ Improved Workplace Safety: Closed-mold operation minimizes exposure to harmful fumes.
Resin Infusion is preferred when lightweight, high-performance, and structurally strong composite parts are required, making it a go-to method for critical applications in demanding industries.
Steps:
- Mold Preparation – The mold is cleaned, treated with a release agent, and prepared with dry fiber reinforcements.
- Vacuum Bag Setup – A vacuum bag is sealed around the mold, and a vacuum pump removes air.
- Resin Injection – Liquid resin is drawn into the fibers through vacuum pressure, ensuring even distribution.
- Curing Under Vacuum – The part cures under controlled conditions, reducing voids and defects.
- Demolding & Trimming – Once cured, the part is removed, trimmed, and polished for final use.
- Final Inspection – The part undergoes thickness, weight, and strength testing for quality assurance.
Ensuring Compliance with Client Specifications
At DIMENGY, we ensure strict quality control throughout the entire manufacturing process to meet client tolerances and specifications with high precision. Our inspection process includes:
- Dimensional Control – Using calibrated measuring tools and 3D scanning for complex geometries.
- Thickness & Weight Verification – Ensuring uniform layer distribution within a ±5% tolerance of specified values.
- Mechanical Testing – Validating strength, flexibility, and impact resistance according to industry standards.
- Surface & Finish Inspection – Checking for uniformity, gloss level, and defect-free surfaces.
By applying continuous monitoring and final validation, we guarantee that each part meets the highest standards of quality, durability, and consistency.